HOW JENSEN PRECAST PREVENTED 120 HOURS OF DOWNTIME WITH WAITES PREDICTIVE MAINTENANCE SOLUTION
Discover how Jensen Precast, a leading U.S. concrete manufacturer, successfully transitioned from reactive to predictive maintenance using Waites' advanced predictive maintenance solution. Jensen prevented more than 120 hours of unplanned downtime and saved more than $30,000 by proactively addressing equipment anomalies.
This detailed case study outlines the rapid, single-day deployment of Waites’ sensors, the crucial role of real-time data and analyst-driven insights, and how Jensen Precast effectively integrated predictive maintenance into their operational strategy.
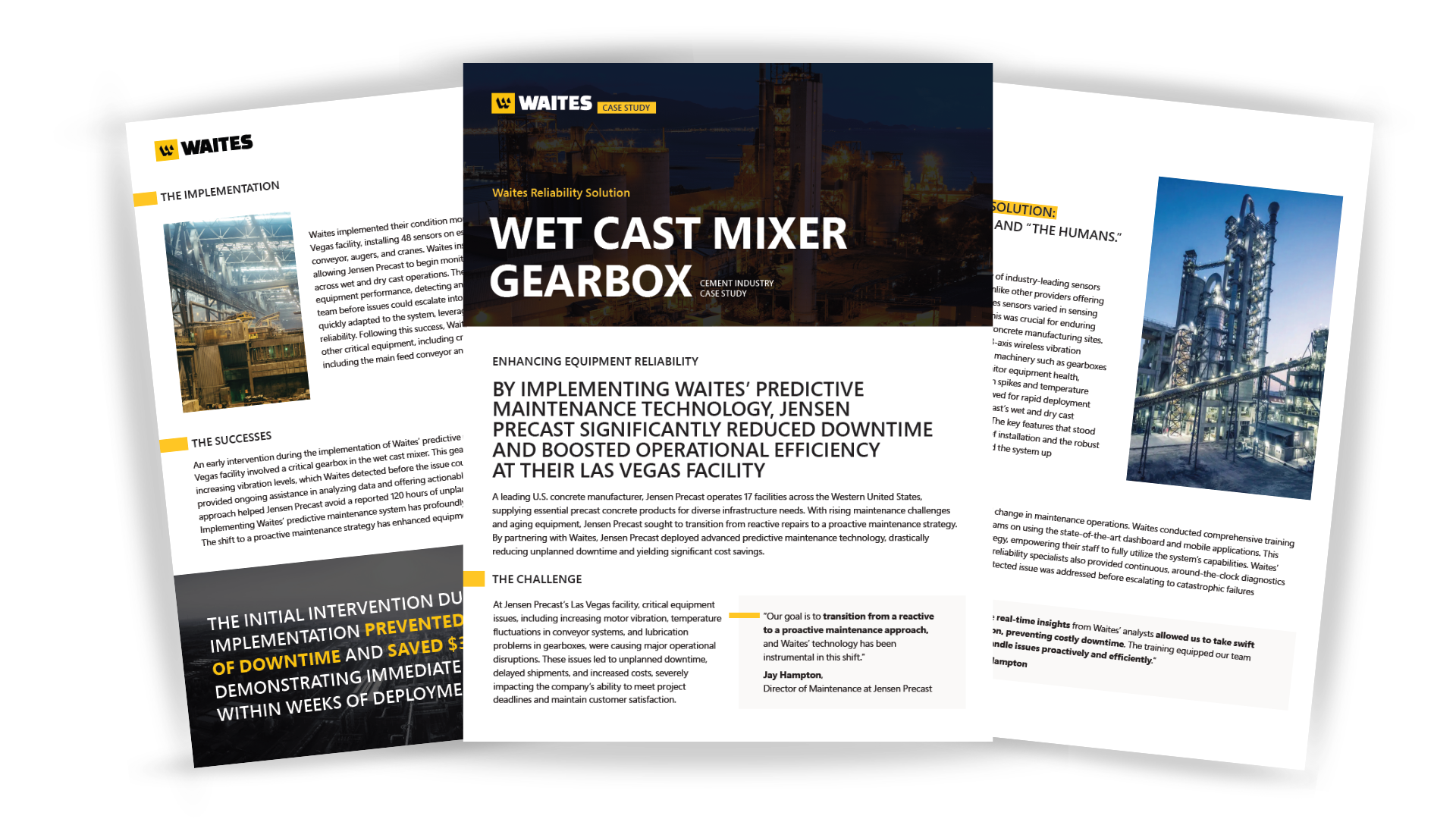
GET YOUR CASE STUDY
WHAT YOU'LL LEARN
- Specific ways predictive maintenance prevented 120 hours of downtime and saved $30,000 at Jensen Precast.
-
How Waites' hardware, tailored to harsh environments, AI, and expert human analysis, worked together to boost reliability.
-
Detailed, actionable steps for real-time anomaly detection and swift, proactive interventions.
-
Why Jensen Precast plans a broader implementation of Waites’ solutions to maintain maximum operational uptime and efficiency across all facilities.